Are you tired of dealing with a leaky tire inflator hose? Look no further! In this article, we will guide you through the simple steps of repairing your tire inflator hose, saving you time and money. Whether you have a puncture or a damaged hose, we’ve got you covered. With our easy-to-follow instructions, you’ll be back on the road in no time. Say goodbye to those frustrating trips to the mechanic and hello to hassle-free tire maintenance. So, grab your tools and let’s get started on fixing that tire inflator hose!
How To Repair Tire Inflator Hose
Table of Contents

Inspecting the Hose
Checking for Leaks
To begin repairing your tire inflator hose, it is important to first inspect it thoroughly for any leaks. Leaks can be easily identified by simply rubbing a soapy solution along the length of the hose and keeping an eye out for any bubbles forming. If you notice any bubbles, this indicates the presence of a leak. Identifying leaks is essential as it allows you to address the problem before it worsens and affects the overall functionality of the hose.
Assessing the Condition of the Hose
After checking for leaks, it’s crucial to assess the overall condition of the hose. Look out for any signs of cracks, tears, or other visible damage. Pay close attention to areas where the hose may have been bent or twisted excessively, as this can weaken the structure and lead to potential issues. By carefully inspecting the hose, you can determine the extent of the damage and the best course of action to repair it.
Identifying Cracks or Damage
During the inspection, keep an eye out for cracks or other forms of visible damage. Cracks can weaken the hose and eventually cause it to break if not addressed promptly. Additionally, look for any signs of wear and tear, such as fraying or thinning of the material. By identifying any cracks or damage, you can take the necessary steps to fix or replace the affected sections to ensure the proper functioning of your tire inflator hose.
Gathering the Required Tools and Materials
Essential Tools
Before you begin repairing your tire inflator hose, make sure you have the right tools on hand. Some essential tools you will need include a utility knife, pliers, a hose cutter, a rubber patch kit, a multi-purpose sealant, and duct tape. These tools will help you carry out the necessary repairs effectively and efficiently.
Recommended Materials
In addition to the essential tools, there are a few recommended materials that can enhance the durability and longevity of your repairs. Consider having a replacement hose section, O-rings, and fittings readily available. These materials can come in handy if you need to replace damaged sections or faulty components during the repair process.
Repairing Small Leaks
Using Duct Tape
If you have identified small leaks in your tire inflator hose, one quick and temporary solution is to use duct tape. Simply wrap a layer or two of duct tape tightly around the area with the leak. Duct tape acts as a temporary sealant, preventing any further air leakage. While this solution may not be a permanent fix, it can buy you some time until you can execute a more thorough repair.
Applying Rubber Patch
For a more long-term solution to repair small leaks, using a rubber patch is recommended. Begin by cleaning the damaged area of the hose with a mild detergent or rubbing alcohol to remove any dirt or debris. Once the area is clean and dry, apply the rubber patch according to the instructions provided with the kit. Press the patch firmly onto the damaged area, ensuring it adheres securely. Allow the patch to cure completely before using the hose.
Replacing a Damaged Hose Section
Cutting Out the Damaged Section
If you encounter a damaged section of your tire inflator hose that cannot be repaired effectively, you may need to replace the entire section. Start by cutting out the damaged portion using a hose cutter or utility knife. Ensure that the cut is clean and straight to ensure a proper fit when attaching the new hose section.
Choosing a Suitable Replacement Hose
When selecting a replacement hose section, make sure it is the correct length and diameter to match your tire inflator and existing hose. It is also important to choose a hose of high-quality material to ensure its durability and resistance to wear and tear. Consider opting for a reinforced hose to enhance its strength and longevity.
Attaching the New Hose Section
To attach the new hose section, start by applying a thin layer of multi-purpose sealant to the ends of both the new hose section and the remaining hose. This will create a secure seal when the two sections are connected. Insert one end of the new hose section into the remaining hose and twist them together firmly. For added security, you can use hose clamps to ensure a tight connection. Make sure to tighten the clamps securely, but not excessively, to avoid damaging the hose.
Fixing Cracks and Tears
Cleaning the Surface
Before repairing cracks or tears in your tire inflator hose, it is crucial to clean the surface thoroughly to ensure proper adhesion of the sealant. Use a mild detergent or rubbing alcohol and a clean cloth to remove any dirt, grease, or debris from the damaged area. Allow the surface to dry completely before proceeding with the repair.
Applying Multi-Purpose Sealant
Once the surface is clean and dry, carefully apply multi-purpose sealant over the cracks or tears using a brush or applicator provided with the sealant. Ensure that the sealant covers the entire damaged area and extends slightly beyond it to create a strong and durable repair. Allow the sealant to cure according to the manufacturer’s instructions before using the hose.
Replacing O-Rings or Fittings
Identifying Faulty O-Rings or Fittings
If you experience air leakage or notice a decrease in the performance of your tire inflator hose, it might indicate a faulty O-ring or fitting. Inspect these components carefully and look for signs of wear, damage, or deformation. Faulty O-rings or fittings can compromise the seal and lead to air leakage.
Removing and Replacing O-Rings
To replace a faulty O-ring, start by gently removing the old O-ring from its groove using pliers or a small screwdriver. Take note of the size and shape of the old O-ring to ensure you get an appropriate replacement. Once the old O-ring is removed, clean the groove thoroughly to remove any residue or debris. Apply a small amount of lubricant to the new O-ring and carefully place it into the groove, ensuring it sits securely.
Replacing Faulty Fittings
To replace a faulty fitting, start by disconnecting the hose from the inflator or other components. Depending on the type of fitting, you may need to use pliers or a wrench to loosen and remove the old fitting. Once the old fitting is removed, clean the threads and ensure they are free from debris. Apply a layer of thread sealant to the new fitting and carefully thread it into place, making sure it is tightened securely.
Maintaining and Preventing Future Damage
Proper Storage of the Tire Inflator Hose
To maintain the lifespan of your tire inflator hose, it is crucial to store it properly. When not in use, ensure that the hose is coiled neatly and stored in a dry, cool place away from direct sunlight. Avoid bending or folding the hose excessively, as this can lead to cracks or weak spots over time. By storing the hose correctly, you can prevent unnecessary damage and prolong its durability.
Regular Cleaning and Inspection
Regular cleaning and inspection are essential to identify any potential issues before they escalate. Clean the hose with mild detergent or rubbing alcohol periodically to remove any dirt, grease, or debris that may accumulate over time. Additionally, inspect the hose for any signs of wear, cracks, or leaks. By addressing any problems promptly, you can prevent further damage and ensure the hose functions optimally.
Avoiding Common Causes of Damage
There are certain precautions you can take to avoid common causes of damage to your tire inflator hose. Avoid dragging or pulling the hose across rough surfaces, as this can lead to tears or abrasions. Additionally, be cautious when using the hose around sharp objects or edges that can puncture or cut the material. By using the hose with care and avoiding potential hazards, you can significantly reduce the risk of damage.
Seeking Professional Help
Complex Repairs
While many repairs can be done on your own, there may be instances where seeking professional help is necessary. Complex repairs that involve intricate components or require specialized tools may be best left to the experts. If you are unsure about the complexity of the repair or lack the knowledge and experience to tackle it yourself, it is recommended to consult a professional tire repair service.
Lack of Experience or Tools
If you are inexperienced in handling hose repairs or do not have access to the necessary tools and materials, it is advisable to seek professional assistance. Attempting repairs without the right expertise and equipment can lead to further damage or ineffective repairs. Professionals have the skills and resources to identify and fix hose issues correctly, ensuring the longevity and functionality of your tire inflator hose.
When Replacement is More Suitable
In some cases, the damage to your tire inflator hose may be beyond repair or the cost of repairing outweighs the cost of a replacement. If the hose is extensively damaged, has multiple leaks, or is showing signs of significant wear and tear, it may be more practical to replace the entire hose. Consulting a professional can help you determine the best course of action and provide guidance on selecting a suitable replacement hose.
Safety Precautions
Disconnecting the Inflator
Before undertaking any repairs or maintenance on your tire inflator hose, ensure that the inflator is disconnected or turned off. This is important to prevent accidental inflation and avoid injury. Always follow the manufacturer’s instructions regarding the safe disconnection of the inflator to minimize any potential risks.
Wearing Protective Gear
When working on your tire inflator hose, it is essential to wear appropriate protective gear. Gloves and safety glasses can protect your hands and eyes from any sharp or potentially hazardous materials. Additionally, wearing long sleeves and long pants can provide an extra layer of protection against any accidental cuts or scrapes.
Maintaining Proper Pressure
When inflating tires using your repaired hose, it is crucial to maintain proper pressure levels. Overinflation can lead to tire blowouts, while underinflation can cause poor vehicle performance and decreased fuel efficiency. Refer to your vehicle’s manual or tire manufacturer’s guidelines to determine the correct tire pressure and ensure that your repaired hose delivers accurate inflation.
Conclusion
Repairing your tire inflator hose can save you time, money, and hassle. By following these steps, you can effectively address leaks, cracks, and other issues, ensuring the proper functionality and longevity of your tire inflator hose. Regular inspection, maintenance, and taking preventative measures such as proper storage and avoiding common causes of damage can help prolong the lifespan of your hose.
When in doubt or faced with complex repairs, do not hesitate to seek professional help to ensure the safety and reliability of your tire inflator hose. Remember to always prioritize safety by disconnecting the inflator, wearing protective gear, and maintaining proper pressure. With proper care and maintenance, your tire inflator hose will continue to serve you well in keeping your tires properly inflated.
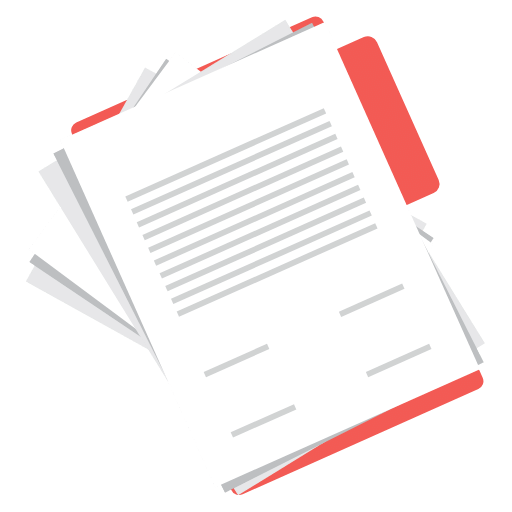
Keep your car tires in peak condition with the right inflator.
Discovering the best tire inflator can be a game-changer for maintaining your vehicle. Explore our comprehensive Ultimate Guide to the Best Tire Inflators to make an informed decision.