Air compressors play a vital role in numerous industries, from construction to automotive repairs. However, understanding the technical aspects of these machines can sometimes be a bit overwhelming. One common area of confusion is the difference between CFM and PSI in an air compressor.
CFM, or Cubic Feet per Minute, refers to the volume of air that the compressor can deliver, while PSI, or Pounds per Square Inch, measures the pressure at which the air is delivered. In simpler terms, CFM represents the flow rate of the air, while PSI indicates the force behind it. In this article, we will delve into the details of CFM and PSI, helping you make informed decisions when it comes to choosing the right air compressor for your needs.
What Is The Difference Between CFM And PSI Air Compressor?
Table of Contents

CFM vs PSI: Understanding the Basics
When it comes to air compressors, two important terms that often come up are CFM and PSI. Understanding the basics of CFM (cubic feet per minute) and PSI (pounds per square inch) is crucial in selecting the right air compressor for your needs. These measurements provide valuable insights into the performance and capabilities of an air compressor, as well as its compatibility with different tools and applications.
Definition of CFM
CFM, or cubic feet per minute, refers to the volume of air that an air compressor can deliver in a minute. It is a measurement of the amount of air that flows through the compressor, indicating its capacity to power various pneumatic tools and equipment. The higher the CFM rating of an air compressor, the greater the volume of air it can deliver.
Definition of PSI
PSI, or pounds per square inch, measures the pressure of the compressed air produced by an air compressor. It represents the force exerted by the air when it is compressed and determines how efficiently the air can perform tasks that require pressure, such as operating air tools or inflating tires. The higher the PSI rating of an air compressor, the greater the pressure it can generate.
Importance of CFM and PSI in Air Compressors
Both CFM and PSI are essential factors to consider when selecting an air compressor for specific applications. The CFM rating determines how quickly an air compressor can supply air, while the PSI rating determines the force with which the air is delivered. By understanding the relationship between CFM and PSI, users can choose the right combination of air volume and pressure to meet their specific needs.
CFM and PSI: Key Differences
To fully grasp the difference between CFM and PSI, it is essential to understand the measurement units used and the distinction between air volume and air pressure.
Measurement Units
CFM is measured in cubic feet per minute, indicating the volume of air delivered. PSI, on the other hand, is measured in pounds per square inch, signifying the pressure of the compressed air.
Air Volume vs. Air Pressure
CFM measures the amount or volume of air an air compressor can deliver, while PSI measures the force or pressure at which the air is delivered. CFM is more relevant when considering tools that require a continuous supply of air, such as paint sprayers or grinders. PSI is crucial for tools that require a higher level of pressure, such as nail guns or impact wrenches.
Applications
The difference between CFM and PSI becomes particularly significant when considering different applications. CFM is vital for tools that require a certain volume of air, such as sandblasters or spray guns, as insufficient CFM can lead to poor performance or inconsistent results. PSI is essential for tools that require a specific pressure level, as lower PSI may result in inadequate force for tasks such as tire inflation or heavy-duty construction.
CFM and PSI: Working Together
While CFM and PSI have distinct meanings, they work together to provide the necessary air volume and pressure for various applications. Understanding the relationship between CFM and PSI is crucial in selecting an air compressor that can effectively power the required tools.
Relationship between CFM and PSI
The relationship between CFM and PSI can be understood by considering the concept of air power. Air power is determined by multiplying the CFM and PSI ratings of an air compressor. For example, an air compressor with a CFM rating of 10 and a PSI rating of 90 would have an air power of 900 (10 CFM x 90 PSI = 900). This means that the air compressor can deliver 900 units of air power to the tools or equipment it supports.
Choosing the Right Combination
To choose the right combination of CFM and PSI for your needs, it is important to consider the specific requirements of the tools or applications you plan to use. Some tools may require a high CFM but a lower PSI, while others may need a higher PSI but a lower CFM. By understanding the requirements and limitations of different tools, you can make an informed decision when selecting an air compressor with the appropriate CFM and PSI ratings.
CFM and PSI in Different Air Compressor Types
Different types of air compressors have varying CFM and PSI capabilities, making it essential to understand their characteristics to select the most suitable one for your needs.
Reciprocating Air Compressors
Reciprocating air compressors, also known as piston compressors, are a common type of air compressor. They operate by using pistons to compress and deliver air. Reciprocating compressors typically offer a wide range of CFM and PSI options, making them suitable for various applications. Higher CFM and PSI ratings are often available in larger reciprocating compressors, allowing for heavy-duty use in industrial settings.
Rotary Screw Air Compressors
Rotary screw air compressors work by using twin screws to compress air. They are known for their efficiency and reliability, making them a popular choice for continuous or high-demand applications. Rotary screw compressors often provide higher CFM ratings, typically ranging from 50 to several hundred CFM, while their PSI ratings are generally lower than reciprocating compressors. The consistent and steady supply of air delivered by rotary screw compressors makes them ideal for applications that require a constant amount of air over an extended period.
Centrifugal Air Compressors
Centrifugal air compressors are designed for heavy-duty industrial applications that demand a large volume of compressed air. They utilize centrifugal force to compress air, resulting in extremely high CFM ratings. However, centrifugal compressors tend to have lower PSI ratings compared to other types. These compressors are commonly used in large manufacturing facilities and power plants where there is a need for large-scale air compression.
CFM and PSI in Various Applications
CFM and PSI ratings play a crucial role in determining the suitability of an air compressor for specific applications. Here are some common applications where CFM and PSI considerations are essential:
Automotive
In automotive applications, CFM is important for tasks such as sanding, painting, inflating tires, and running air tools. PSI is crucial for tasks like impact wrenching, where higher pressure is necessary to remove stubborn nuts and bolts.
Construction
In the construction industry, CFM is vital for powering pneumatic tools such as nail guns, drills, and sanders. Higher CFM ratings are often required to handle heavy-duty tasks efficiently. PSI is important for tasks like concrete demolition, where high-pressure air is needed to break up solid materials.
Woodworking
Woodworking applications often require CFM for tasks such as sanding, painting, or operating pneumatic woodworking tools like saws and routers. PSI is crucial for tasks like driving nails or staples into hardwood, where higher pressure ensures secure and effective fastening.
Spray Painting
In spray painting applications, CFM is important for providing a consistent air supply to achieve an even and smooth finish. PSI is crucial in achieving the desired pressure for proper atomization of the paint, resulting in a professional-quality paint job.
Industrial
In industrial settings, CFM and PSI requirements can vary greatly depending on the specific application. From powering heavy machinery to operating pneumatic systems, a careful consideration of CFM and PSI ratings is necessary to ensure optimal performance and productivity.
Factors Affecting CFM and PSI Ratings
Several factors can affect the CFM and PSI ratings of an air compressor. Understanding these factors can help users make informed decisions about the size and capabilities of an air compressor.
Air Compressor Size
The physical size of an air compressor can affect its CFM and PSI ratings. Generally, larger air compressors tend to have higher CFM and PSI capabilities, making them suitable for heavy-duty applications. However, it is important to balance the size and power requirements to avoid over or underestimating the necessary capacity.
Air Receiver Tank Size
The size of the air receiver tank in an air compressor can impact its CFM and PSI ratings. A larger tank allows for more air storage, reducing the strain on the compressor and providing a steady supply of air. This can be beneficial for tools or applications that require frequent bursts of air.
Air Quality and Temperature
Air quality and temperature can also affect the CFM and PSI ratings of an air compressor. Contaminated air or high ambient temperatures can influence the performance and output of the compressor, potentially decreasing the CFM and PSI capabilities. Proper maintenance, including regular cleaning and maintenance of air filters, can help maintain optimal performance.
Understanding CFM and PSI Ratings
To make the most of CFM and PSI ratings, it is important to have a solid grasp of their implications and how they relate to specific tools and applications.
Decoding CFM Rating
When considering the CFM rating of an air compressor, it is important to look for both the free air CFM rating and the CFM delivered at a specific PSI (often referred to as SCFM or Standard Cubic Feet per Minute). The free air CFM rating represents the maximum amount of air the compressor can deliver without any restrictions, while the SCFM rating takes into account the pressure at which the air is delivered.
Decoding PSI Rating
The PSI rating of an air compressor indicates the maximum pressure it can generate. However, it is important to note that the PSI rating does not reflect the actual working pressure required for specific applications. Some tools may require a lower working pressure than the maximum PSI rating, while others may need a higher working pressure for optimal performance. Understanding the requirements of the tools and applications is key to selecting the appropriate PSI rating.
Common CFM and PSI Chart for Air Tools
To provide a general guideline, here is a recommended CFM and PSI chart for common air tools:
- Air Sander: 6-10 CFM at 90 PSI
- Impact Wrench (1/2-inch): 4-9 CFM at 90 PSI
- Angle Grinder (4-inch): 5-8 CFM at 90 PSI
- Brad Nailer: 0.3-1.2 CFM at 70-90 PSI
- Paint Sprayer (HVLP): 4-8 CFM at 40 PSI
- Tire Inflator: 2-3 CFM at 90 PSI
These are general guidelines and can vary depending on the specific brand and model of the tool. Always refer to the manufacturer’s recommendations for the most accurate CFM and PSI requirements.
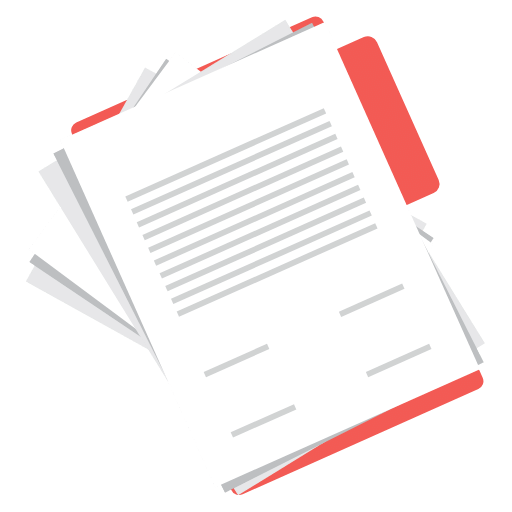
Keep your car tires in peak condition with the right inflator.
Discovering the best tire inflator can be a game-changer for maintaining your vehicle. Explore our comprehensive Ultimate Guide to the Best Tire Inflators to make an informed decision.
Factors to Consider when Choosing an Air Compressor
When selecting an air compressor, several factors should be taken into consideration to ensure it meets your specific needs and requirements.
Required Air Volume and Pressure
Consider the CFM and PSI requirements of the tools and applications you plan to use. Determine the minimum and maximum CFM and PSI ratings needed to adequately power your tools and select an air compressor that meets those requirements.
Usage Frequency and Duration
If you plan to use the air compressor frequently or for extended periods, it is important to choose a compressor with a higher duty cycle. A higher duty cycle indicates the compressor can run for a more extended period without overheating or requiring cooldown breaks.
Available Power Source
Consider the available power source at your desired location. Air compressors can be powered by electricity, gasoline, or diesel. Choose the power source that suits your needs and the availability of the fuel or power supply.
Portability and Noise Level
If you require mobility or plan to move the air compressor between different job sites, consider the portability and weight of the compressor. Additionally, take into account the noise level of the compressor, particularly if using it in residential or noise-sensitive areas.
Budget
Finally, consider your budget and the investment you are willing to make in an air compressor. Determine your requirements and prioritize the features and capabilities that are most important to you within your budget constraints.
Conclusion
Understanding the difference between CFM and PSI is crucial in selecting the right air compressor for your needs. CFM represents the volume of air delivered by the compressor, while PSI indicates the pressure of the compressed air. The relationship between CFM and PSI is essential in determining the air power and compatibility with various tools and applications. By carefully considering the CFM and PSI requirements of your tools, understanding the different types of air compressors, and taking into account various factors, you can confidently choose an air compressor that meets your specific needs and facilitates optimal performance.
